In addition
cutting open the house to fit a new duct, I had to modify the cabinet to fit the new microwave. Because the microwave was on order, I found installation instructions online and used them to layout the bottom. I had to drill new mounting holes and a rectangular cutout for the duct, neither of which was especially difficult and further simplified by having the cabinet off the wall. Continue readingTag Archives: kitchen
Kitchen Exhaust–Assembling the Duct
Rectangular metal duct connects the holes in my kitchen ceiling and exterior wall. I assembled the duct out of three-foot long flat sections, folding two pieces into ell-snapped walls and joining those to form a section of duct. To join the two sections I needed together, I used S-cleats on the long sides drive cleats on the short sides as outlined here. I then sealed the seams with mastic, which seemed to take forever to dry. For the long seams, I opted to use a high-quality foil tape, an approach I’ll use for any future duct work I do given its ease of use and instant gratification. Continue reading
Kitchen Exhaust–Preparing for a New Duct
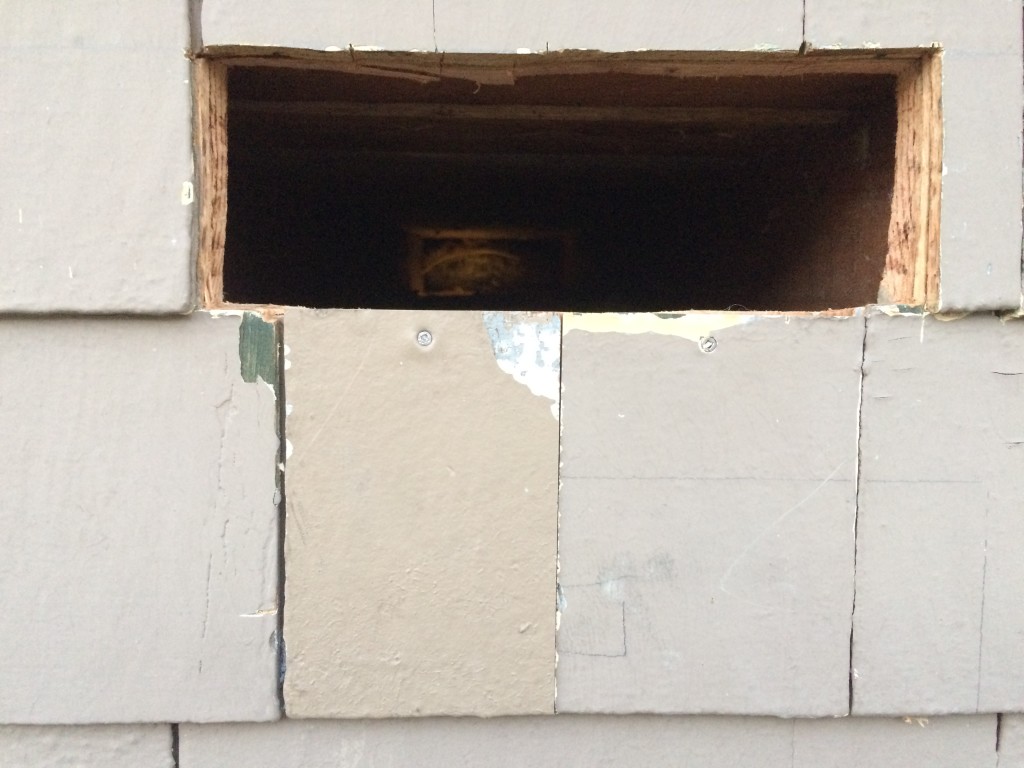
Cutting a hole in your house is a bit troubling. Here I’ve squared my opening. A hint of the house’s original green stain is visible on a shingle on the bottom right of the cutout.
Installation of a waterline for an ice maker was prompted by the purchase of a new fridge, which in turn entailed replacing the stove and over-the-range (OTR) microwave to ensure matching finishes (fortunately the dishwasher was an integrated model and concealed behind cabinetry).
Ice Maker Waterline
After a decade of frozen drain lines and inner shelves dripping with water, we were ready to retire our old fridge. We were also ready to retire our ice trays–it was past time to install a waterline for an ice maker. After completing the work in hours, I regretted not doing in much sooner. Continue reading
Glass Tile Backsplash–Installation
Installation
Having tiled with ceramic tiles, I expected using glass to be very similar. That expectation was met. The reading I did beforehand (This Old House and DIY network were especially useful) suggested special care to avoid scratching the tile’s show surface and to accommodate glass’s translucent characteristic. In practice, I found the glass tile not especially prone to scratching, and the opaque color applied to the back meant my thin set lines didn’t telegraph through the tile, so quickly gave up on knocking them down. The one place I did take special care throughout the project was when cutting tiles–they seemed more prone to chip out than ceramic tiles, so when making cuts, I would cut in from one edge slightly then flip the piece over and finish the cut.
Layout is perhaps the most important aspect of a tiling project, and the kitchen set up made that task easy for this project. I worked in from each exposed edge toward either a corner or bank of cabinets and was able to run 7 full courses of tiles up the wall. The irregular vertical positioning of outlets made for some awkward cuts, but we were still able to install the entire backsplash, grout, and caulk over four days.
Tools and Materials
- 2″ x 4″ glass tile by MSI
- an inexpensive wet saw
- white thinset for glass tiles
- 1000 grit sandpaper to polish sawn edges
- 1/4″ x 3/16″ V-notched trowel
- masking tape
- drop cloth
- grout float
- unsanded grout (bone color) and matching caulk
- 5 gallon bucket for mixing
Glass Tile Backsplash–Before
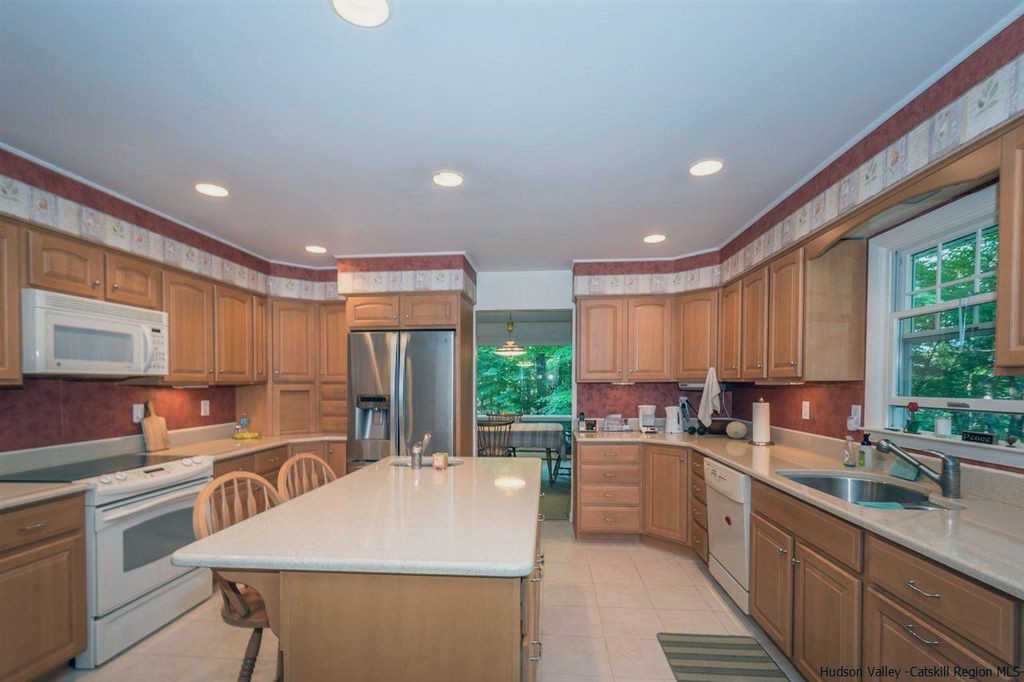
The renovated kitchen in my sister-in-law’s kitchen included a wall paper treatment featuring marbled burgundy and floral border. Image via Zillow.
Over the holidays, my wife and I installed a glass tile backsplash in my sister-in-law’s new house, replacing the wallpaper installed by a previous owner as part of the kitchen renovation. Although labor intensive, it’s not too technically challenging a project. It helped that they’d stripped the wallpaper and scuff sanded the sheetrock beneath to provide tooth for the thin-set we used to adhere the tile.
Kitchen–Dishwasher Install
After three years and approximately 10,000 dishes washed by hand, we finally decided to install a dishwasher. We’d always planned on it–had, in fact, left a bank of drawers empty in anticipation of replacing them–but it was a low priority. The space available wasn’t quite large enough for a 24″ model, limiting our search to 18″ models. As it turns out, the pool of candidates was limited to one cheap model, one mid-range model, and two ridiculously expensive models. A cost-benefit analysis showed spending the money for the mid-range Bosch was worth it for a stainless steel tub, hidden controls, and quiet operation. Continue reading
Kitchen floor
We successfully ignored the vinyl floor in our kitchen for two years. It wasn’t offensive (although the white did tend to show dirt quickly). It even matched the tile backsplash. But floor in the living room appeared to run interrupted underneath the vinyl, suggesting the fir continued into the kitchen. While my wife was out of town for a week, I pried up the transition strips, slid a putty knife under the vinyl and tore up a strip while hoping the fir didn’t end butted up against a sheet of plywood or had rotted. Continue reading
Kitchen–Cabinet Doors
I was hanging the second of my newly built kitchen cabinet doors, a simple frame-and-panel, paring a hinge mortise when I realized the full weight of the task in front of me. One door hung, one more that would be hung . . . eventually. I shaved off another paper thin layer of wood, then looked up and counted the number of doors that needed to be hung. Only fourteen more to go. I swore quietly to myself and checked the fit of the hinge in its mortise. Continue reading
Build a Leaded Glass Panel
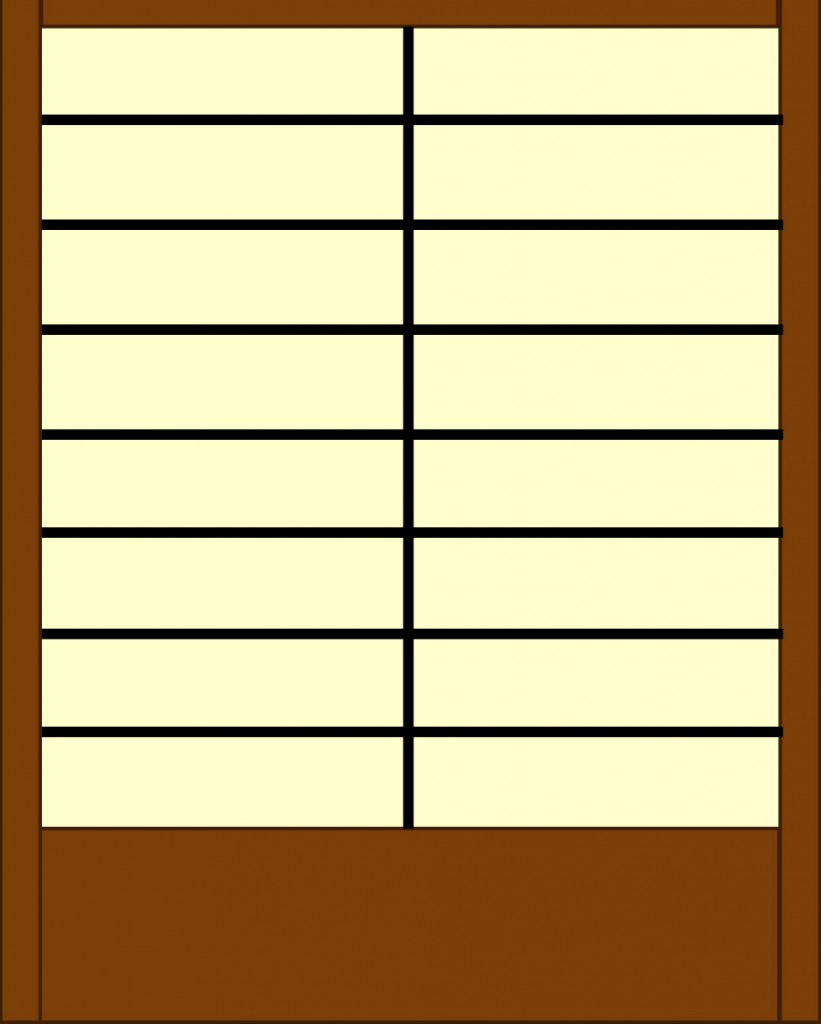
Straight cuts allow for plenty of design variation while allowing for easy construction. Here the choice of frame, color of glass, and thickness of came combine to suggest a shoji screen.
On the local Historical Society’s annual tour of homes, we admired the leaded glass paneled doors of a kitchen’s cabinets and decided to do something similar as part of the update to our kitchen. While
cutting and fitting curved pieces requires special equipment, the straight edges used here are easily assembled using only a few additions to common shop tools. Simple variations adapt the panels to a variety of styles, including Craftsman, Prairie, and Asian-inspired.
To build your own panels, you’ll need a glass cutter, straight edge, solder, came, a way to cut the came (I used a power miter saw, but a hacksaw will work), glass, putty, putty knife, and an assembly board, a large rectangle of MDF or plywood with two fences forming a right angle at one corner of the board. The panel is assembled from that corner outward, ensuring tight fitting joints and a square panel as glass and came are added to achieve the desired size. The panel is then soldered and puttied. Read more.