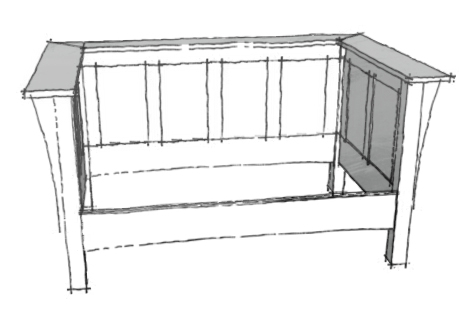
A variation on L & J. G. Stickley’s No. 220. settle. I’ve shortened the length and added a slight arch to the long stretchers.
I’ve admired Leopold and John George Stickley’s “Prairie Style” settle since I first encountered it in Bob Lang’s Shop Drawings for Craftsman Furniture, so my thoughts turned to it when we began to consider replacing some seating in our living room. We needed something shorter, though, so I determined how much space I had, then adapted the Stickley design. Continue reading