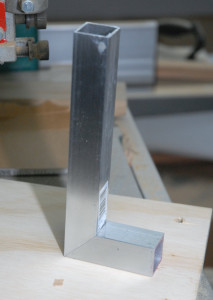
I’d read in the past that you can use woodworking tools to mill soft metals like brass and aluminum, but I didn’t give that much thought. I also read you can bond metal using epoxy. Again, I didn’t give the fact much thought–until recently. Researching an upcoming project, I’ve finally had cause experiment with epoxy and aluminum tubing, and with my first results, my reaction has gone from “oh, you can epoxy aluminum” to something like “HOLY @#!$! YOU CAN EXPOXY ALUMINUM!” No need to braze or weld, you can just glue. Couple that capability with the ability to mill soft metals using woodworking tools, and it opens up new potential in the shop.
I’m still in the early stages of my experimentation, practicing simple and compound miter joints, but it’s a short step from experiment to fabricating parts. The base of a Nelson bench comes to mind, as does a variation on an Eames surfboard table.
To build the miter:
- Cut the aluminum tubing at the miter saw.
- Sand the miter with 50-80 grit paper. Scuffing the metal helps the epoxy adhere to it.
- Clean the metal with mineral spirits.
- Mix epoxy per the instructions. I used JB weld.
- Apply the epoxy yo the tubing and clamp together. I used a corner clamp for this miter, but for a trapezoidal frame (like the base of the Nelson bench, I’ll try packing tape.
More Information