After considering a couple of 3D models of the leg options, I built the basic leg since I could always modify it. After routing out the first of the legs for the table, I decided the simple 3/4″ thick option wouldn’t look as good as a variation on the laminated leg. A practical consideration underlines the visual appeal of the laminated leg as well–the extra depth provides a better seat for the apron tenons. Instead of a simple triangular piece glued to the main leg, I sawed down a copy of the main leg to produce a slimmer profile. This has the the benefit of producing depth for the stretcher tenon. The edge of the piece is rabbeted to produce a 1/4″ tongue that is house in a corresponding groove in the main leg.
Tag Archives: 2014
A Tale of Two Legs
It turns out I didn’t have to look far to find an alternative to the turned legs in the Juhl coffee table I’m working on. There’s a tapered leg Juhl used in an ottoman design and in a coffee table design. While I’m contemplating a variation, though, I may as well contemplate a variation on that variation. I like the accent strip featured on the inside of the leg since it gives that profile a little more dimensionality. It also helps balance the structure.
The taper, though, calls to mind some Shaker designs, and I find myself considering eliminating the strip and beveling the leg from 3/4″ thickness at the top to 1/2″ at the bottom. The side stretcher looks a little less grounded, then, but the stark taper isn’t without its appeal, and it’s also easier to execute. Decisions, decisions.
Finn Juhl Coffee Table–Design
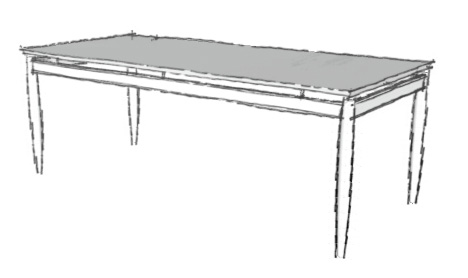
Finn Juhl’s design features a beveled top suspended above a simple base distinguished by turned, tapered legs.
For my next project I’m jumping out of my usual Arts & Crafts period work several decades to build a Mid-century Modern coffee table by the Danish designer Finn Juhl. Juhl’s table features a beveled top suspended above its base by six dowels. Turned, tapered legs distinguish the rectilinear base.
The coffee table, along with sideboard, is perhaps the signature piece of mid-Century furniture, in much the same way the Morris chair has become emblematic of Arts & Crafts furniture. And Juhl’s table is an intriguing example of the form. He used the floating top elsewhere in his designs, but more often in his chairs, making its appearance as a table top a bit of an aberration. The original was built of teak, but I’m contemplating a version in fir or cherry, depending how closely I want to hew to the original construction, which features a veneered top banded with solid wood edging. If I follow suit, I’ll use some cherry plywood left over from an old project. If I opt for a solid wood top, I’ll be able to use some wide fir boards I picked up when a local sawyer moved shop to Alaska. Of course a solid wood top creates the potential for movement problems with seasonal changes in humidity, but I think there’s enough flex in how the top joins the base to absorb that movement. Continue reading
Trellis–Construction
The hardest part about completing the trellis was managing the slope of the patio. I began construction by laying out the notches for the joinery on 5/4 x 4 cedar boards, then began cutting the notches–36 in all. I took that effort in stages, beginning with the horizontal boards. I began by defining each edge of the notch with my dozuki, then making a couple of additional cuts across the notch, then popping the waste free with a chisel and paring the joint relatively even. Cedar is easy to work by hand, so this went fairly quickly, but I was ready to try the router when it came time to notch the vertical members. Continue reading
Trellis–Design
I am, perhaps, too enamored of shoji, but I find the potential for the arrangement of kumiko intriguing. So I immediately thought of shoji when tasked with building a trellis for the climbing hydrangea growing at one corner of our porch. I’d originally planned to reproduce the design of my fence lattice, but the 1″ width seemed a little insubstantial for the space. I changed the width to 1.5″ and echoed the double strips separated by a strip width in the fence lattice. Then it was a matter of playing with the arrangement until I found a silhouette I liked.
No. 220 Settle–Corbels
The corbel is a common element in Craftsman furniture, providing form and function. A series of corbels supports the wide arms of the No. 220 settle. Five are required for my shortened version: one on each front leg, two on each rear leg, and one centered on the back. While the No. 220’s design allows for simply gluing the corbels to the legs (there’s substantial long grain to long grain exposure for good gluing), I chose to join the corbels to the frame using a 1/4″ tongue in the dado to ensure positioning. When replicating corbels for a reproduction, I don’t try to copy it exactly. Instead, I note major dimensions–the width and height of the corbel–and the general shape of the curve, then approximate the curve using a bezier curve in Illustrator or SketchUp. Once I have a shape I like, I print out and transfer to my template. After cutting close on the bandsaw, I complete final shaping with a spokeshave to ensure a fair curve. With the template ready, I mark the blanks, rough out on the bandsaw, then use a pattern bit in the router to copy the parts.
A Modified L & J. G. Stickley Settle–Design
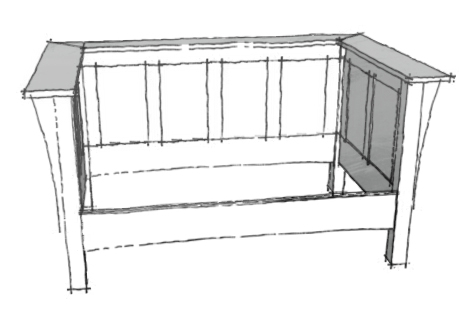
A variation on L & J. G. Stickley’s No. 220. settle. I’ve shortened the length and added a slight arch to the long stretchers.
I’ve admired Leopold and John George Stickley’s “Prairie Style” settle since I first encountered it in Bob Lang’s Shop Drawings for Craftsman Furniture, so my thoughts turned to it when we began to consider replacing some seating in our living room. We needed something shorter, though, so I determined how much space I had, then adapted the Stickley design. Continue reading
L & J.G. Stickley’s No. 220 Settle
I sometimes wonder whether the Stickley brothers ever gathered as a group in adulthood. I picture them, perhaps sitting down to Thanksgiving dinner, or watching their children open Christmas presents, and imagine the undercurrents and tensions that likely arose when five brothers–Gustav, Leopold, John George, Albert, and Charles–all engaged, in various combinations of partnership, in the same profession with varying degrees of success in New York and Michigan–came together in a single place. Shared meals could have been especially fraught after Gustav’s bankruptcy and short-lived association with Leopold and John George’s company. The latter two brothers built their company on designs in the same style as Gustav’s Craftsman furniture before adapting to changing tastes. While the No. 220 settle shows a Craftsman influence, it is, as Bob Lang observers in Shop Drawings for Craftsman Furniture unlike anything produced by Gustav Stickley. Continue reading