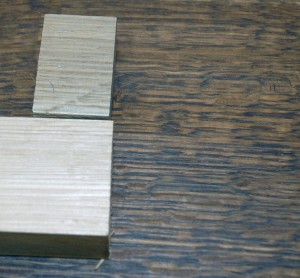
Clockwise, beginning with the small offcut: fumed oak, fumed oak and boiled linseed oil, and unfinished.
Flatsawn–cut so that the tree’s annular rings run parallel to face of the board–white oak is less than distinguished, featuring a porous grain and and a course figure. Take the same log and quarter saw, or slice it so the annular rings rung perpendicular to the board’s face, the wood takes on a whole new character, showing a vertical grain overlayed with the flecked pattern of the tree’s medullary rays. And fuming the wood–exposing it to the fumes of ammonia–creates a chemical change in the wood as the ammonia reacts with tannic in the heartwood to darken it. A top coat of finish completes the effect, leaving the wood a rich, warm brown.
To fume, I first sand through the grits to 220, then drape the piece in plastic sheeting. You can build a frame using 1×2 stock and staple the plastic to the frame, but the simple tent yields similar results and requires less effort. After putting on goggles, a respirator, long sleeves, and gloves, I pour the ammonia into pie plates and place under the tent. Offcuts placed in the tent with the project can be used to gauge how the process is going: a quick wipe of boiled linseed oil reveals the final color. I’ll check back and pull the ammonia when satisfied. A simple oil finish topped by dark paste wax can be quite striking, and a couple of coats of garnet shellac can have a nice effect, too.
More Information
Taunton’s In the Craftsman Style contains a good article on fuming by Kevin Rodel.